‘How Dense Are You?’ :
Recording bloom density
from experimental iron smelting.
INTRODUCTION
Charting the density of a sample group of 30 iron blooms,
created over a span of roughly 15 years during experiments
aimed at understanding iron smelting furnaces, and comparing
these to a number of artifact samples.
The focus of the bloomery iron smelting
undertaken by the team from the Dark Ages Re-Creation
Company, here at Wareham, Ontario, Canada, has been
towards Northern European prototypes, primarily those from what
has been alternately called the ‘Migration Era’ or ‘Dark Ages’;
so ‘Post Roman to Early Medieval’ era (roughly 400 - 1100 AD).
At the risk of being overly simplistic, those ancient furnaces
were generally smaller diameter (25 – 50 cm interior), short to
medium shafts ( estimated at 50 to 100 cm), bellows blown, and
slag tapping. Over two decades of experimental investigations, I
have personally undertaken or been directly involved with 90
bloomery iron smelts, with dozens more observed. Tests have
included a number of extended series investigating Viking Age at
Vinland (total 8), Viking Age Icelandic (total 12), Pictish
(total 7) and Celtic Iron Age (total 4). (1)
It is important to remember that the initial
work here was aimed at testing individual elements leading to an
effective furnace design and establishing a working method, that
together would lead to dependable production of iron blooms.
Later, individual modern aspects would be replaced with more
historic ones, in an attempt to reverse engineer back towards
potential ancient systems and methods.
IRON SMELTS
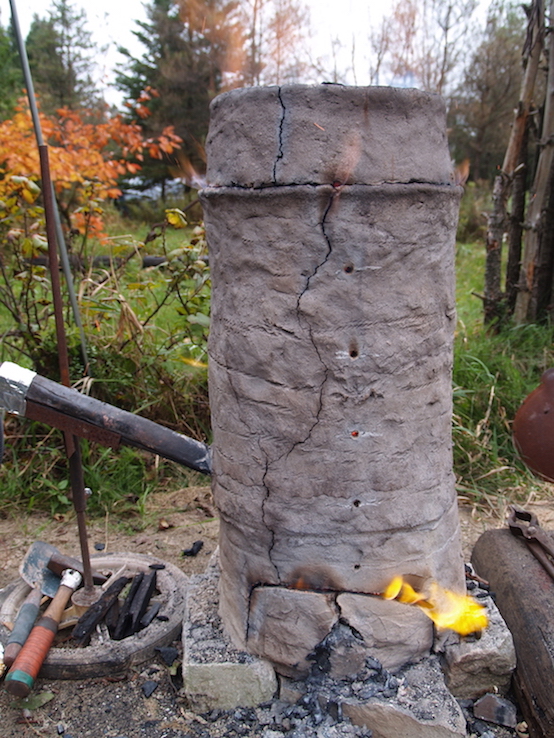
Figure 1 : A fairly typical furnace used in
this experimental series. (experiment # 90 - ‘Wind
& Weathering’, October 2021)
The furnaces built and smelts undertaken have the following
characteristics :
• Furnaces are a ‘short shaft’ type, typically
25 - 30 cm interior diameter (ID), and in the range of 60 - 70
cm tall.
• Primarily clay cobb construction, most using
a standard mix of powdered clay / course sand / shredded horse
manure (dry thirds by volume).
• Slag management has been primarily ‘slag
tapping’ (although some tests of slag contained and slag pit
types have been undertaken).
• Most typically insert style tuyeres,
earliest of steel pipe, from 2005 prepared ceramic tubes, and
since 2012 almost exclusively heavy copper. There have also been
a number of experiments utilizing the ‘bellows plate / blow
hole’ arrangement. (2)
• A variety of ore types have been used, but
from 2008 onwards mainly using a ‘bog ore analog’ consisting of
red oxide powder (Fe2O3) mixed with whole wheat flour as a
binder, with Fe concentrations in the range of 51 - 54 %.
• Locally available commercial Maple or Oak
charcoal as the fuel.
• Final bloom extractions have both been
bottom / side (via a prepared arch) or from the top, normally
without breaking down the furnace structure.
• A fairly standard method of pre-heating,
adding charges of charcoal and ore, to final burning down before
extraction is followed. (3)
During the early years, particularly working
with Lee Sauder and others at the annual Smeltfest
workshops, individual smelts were in the 45 kg of ore range,
which in turn resulted in blooms at 8 - 12 kg. Tests done here
in Wareham (where accessing ore was a problem) more typically
ran 25 - 30 kg ore, with resulting blooms averaging between 3 -
5 kg. It was considered true that if a smaller bloom could
be produced, continuing to a larger one would primarily just
require additional materials, time and effort. It should be
noted that past experience has found that with larger ore volume
smelts, overall yields and bloom densities have also been found
to increase (at least before compaction effects).
Another reason for keeping to smaller blooms
was ease of handling during the secondary compaction of blooms
down into working bars. There is a physical limit to how much
impact force (largely untrained!) workers can apply with hand
sledge hammers. Even historically, once blooms got much over
about 5 - 8 kg, they were commonly cut up into smaller chunks to
allow effective compaction into the finished iron bars. (4)
There are functional limits at roughly 8 – 10 kg, imposed by
human power limits; bellows operation to required air volume,
raw hammering force, and the problems of subsequent re-heating.
(Although larger blooms certainly can, and definitely were,
produced.) (5)
Sauder and Skip Williams had
investigated the use of high volume air in similar sized
bloomeries, clearly illustrating how this impacted by increasing
both bloom density and overall yields (6), and this work had a
large impact on the Wareham experiments.
Most smelts use an electric blower for air supply with which the
expected yields of iron from ore (in smelts as described above)
is in the range of 20%. It is well understood that air delivery
from high volume electric blowers will not accurately duplicate
that from human operated bellows in a number of aspects. There
have been a number of tests using various human powered bellows
types (total 15). The most dependable bellows unit delivers in
the range of 500 - 550 litres per minute (LpM). (7) Electric
blowers are regularly used primarily because of the general
difficulty to organize the significant labour pool required
using a specifically Viking Age type, twin chamber bellows.
Figure 2 : Ken Cook using the second
test ‘smelter’ bellows built in 2008, shown in use for
experiment 42 (‘Vinland
3’, Nov. 2009)
This is considered a significant element to
this report, as the there is no archaeological evidence for
exact design and sizes for bellows specifically used for iron
smelting during the reference period. (8) There are some general
estimates that have been made on what air volumes may have been
required (into the range of 350 LpM for a furnace at 25 cm ID).
(9) The experience at Wareham has been that at those lower
suggested volumes, iron is most certainly produced, but
the blooms created show both low overall yields and a lacy
consistency (which becomes problematic at the bloom to bar
phase) (10)
BLOOMS
The cornerstone reference work, Radomir
Pliener’s ‘Iron in Archaeology - the European Bloomery
Smelters’ gives the following :
“About
90 blooms or parts of blooms had been cut through in order to
observe the consistency of the metal. In 34% of the cases, the
iron was unconsolidated, the block consisting more or less of
sintered-together iron sponge with many isolated grains,
metallic fibres and nodules embedded in a slag matrix. Some
30% of bloom finds were partly consolidated, and had evidently
undergone primary reheating and were partly or wholly forged
and shaped mostly into the loaf form, sometimes with flattened
sides, but with their interiors still full of entrapped slag,
so that further forgings would have been necessary to obtain a
workable material for the manufacture of artifacts.” (Pleiner,
2000, pg 244)
Figure 3 : Disk cut cross section of a typical bloom
measured in this study, half of 6.8 kg.
(experiment # 22 - ‘Redemption’,
Nov. 2006) Note the relatively few internal voids exposed.
Generally, all the blooms produced here at
Wareham are all 'finished' to the same level, which does make at
least comparisons between them valid. Given the small working
team, with normally only myself as having any significant
blacksmithing experience, (11) we hammer work any bloom through
only the one heat cycle available at extraction. This
process involves first knocking off any clinging slag, then very
rough compaction to force the loose exterior metal into the
core. As temperatures are rapidly dropping while all this is
happening, there is rarely very much actual hammer welding
taking place, more the collapsing of larger voids and
forcing out still fluid slag. Although different
individuals may take part as strikers between individual smelts,
the hammers used are identical, so the variation in overall
force applied is likely to be relatively consistent.
Starting in 2012, there was a 30 ton
hydraulic press available at Wareham (a modified
log splitter). In some cases, after the initial hand
hammering, blooms were rushed to the workshop and the mass was
given several compressions, then if possible, cut, all via the
press. Given the initial slag removal and compression is still
undertaken by hand, and the distance from the smelting area to
the press, blooms are at best ‘into the low orange’ visible heat
range by the time they are subjected to the press. It is only
the massive force available that allows much further
modification to be possible. It is worth remembering that
although an extracted bloom is ‘as hot as it ever is going to
get’, this temperature is quickly dropping over this described
sequence.
Figure 4 : Initial hammering of a freshly extracted bloom.
(L – R) Ken Cook, Sam Fallezone, Darrell Markewitz.
(experiment 42 - ‘Vinland 3’, Nov. 2009) Image by Vandy
Simpson
All this suggests that the blooms detailed
below should generally conform to the ‘30% of finds’ described
by Pleiner (above) as ‘partially consolidated’.
Although it is most certainly true that
making any evaluations of artifact blooms from published
photographs is chancy at best, knowing how process has resulted
in surface features after working / observing the creation of so
many blooms at least gives some indications.
There are three characteristics that might be
considered important to assessing the overall effectiveness of
an individual iron smelt, and the ‘quality’ of the iron bloom
produced :
Yield
: At it’s simplest, a measure of effort and raw materials
input against metal output. It has become clear that there is
a certain amount of ore required to create the working slag
bowl system before any metal can functionally accumulate.
(Those researchers who concentrate only on slag and it’s
chemistry most often completely fail to understand this.)
Early production of lacy iron film inside a slag matrix may
indicate an iron reduction process, but does not in
any way illustrate actual bloom production. Our own
experience is that roughly 8 kg of ore (modified by ore iron
concentration / silica content), within furnace diameters used
in these tests, is required to create a truly functional slag
bowl system. (12) As mentioned earlier, potential yield is
greatly effected by total ore additions. Once bloom collection
begins, additional ore continues to add more mass, so a
doubling ore beyond that threshold not only will double the
bloom weight, but also double the effective yield. Ancient
iron makers could be expected to want the very best returns
from their efforts (adjusted by the real problems of working
massive blooms).
Density :
Beyond compaction, how dense a given bloom may be will be is
the result of two primary factors; the number and size of any
internal voids, and how much slag remains trapped within the
metallic mass. It must be remembered that the desired end
product is not the bloom itself, but the working bar compacted
from that bloom. Early experimenters had reported bloom to bar
returns ranging from 80 % to as low as 40% of the starting
‘bloom’ weight. (13) Obviously, the more dense any bloom is,
the less work will be required to weld closed existing voids
and expel remaining slag. In practice, an ancient smith is
most likely to assess density through appearance and
experience in ‘heft’. It should be noted that one secondary
effect of the segmented blooms common through the Viking Age
is that the cut surfaces expose the consistency over the
centre of a bloom.
‘Hardness’
(Carbon Content) : This is suggested to be essentially a
modern concept. It always needs to be remembered that the end
product desired by ancient makers would be primarily lower
carbon, so therefore easier to forge, ‘soft’ iron. Although
higher carbon contents (still less than 1%) are better for
durable (hard) cutting edges, creation of ‘bloomery steels’
would have been accidental at best. (14) If nothing else, the
common method of inserting hard ‘steel’ edges into larger tool
bodies composed of softer iron should indicate this. It needs
to be remembered that the only way an ancient smith could
assess carbon content would be through experience, based on
subtle colour changes to the metal and the ‘feel’ of differing
materials under hammer strokes.
One major problem in this report is that finding actual recorded
densities for artifact blooms has proved extremely difficult.
Weights are certainly available, but at best only the roughest
dimensions are given (typically just a maximum length and
width), but as blooms are complex three dimensional shapes,
these do not allow for any calculations. (15) In some general
(private) discussions with both working archaeologists and
scientifically trained individuals, the reasons that this might
be the case become clear:
The
simplest method of measuring volume is through water
displacement, in fact the method undertaken for this report.
The problem is that emersion in water is most certainly likely
to promote even further corrosion of what are at the very
least ‘uncommon’ artifacts. (16) One potential intervention
(suggested by Tim Young) would be to place the
artifact bloom inside some combination of both durable (blooms
have ragged, often sharp, edges, depending on amount of
compaction) yet flexible, wrapping. This however is certainly
to result in at best ‘ball park’ estimates, as any voids or
surface imperfections would not be included.
A variation on
liquid displacement might prove possible by replacing water
with some volatile liquid that would quickly evaporate,
perhaps something like acetone (?), however this is more a
thought exercise than a practical suggestion. A concern that
introducing any chemical to the surface of the bloom would
seriously impact on the accuracy of later detailed analysis.
(For the liquid suggested for example, any remaining charcoal
embedded would have potential carbon 14 dating rendered
useless.)
A
suggestion given by David Wentz would be an ‘inert gas
displacement pyconometery system’. This equipment is certainly
beyond the reach of almost any field archaeologist. (17)
Another suggestion
(by several individuals) was the use of a 3-D scanner.
Combined with suitable computer software, these systems should
be able to easily produce at least an accurate estimate of the
surface into volume. ‘Small scale / economy’ units are however
fairly recent. I would expect increasingly universities and
museums would have by now invested in such units. Balanced
against this is the fact that the majority of artifact blooms
were excavated well before the existence of the related
technologies. (18)
SAMPLE ARTIFACTS
For comparison, three artifact blooms are
reported by Arne Espelund in ‘The
evidence and the secrets of ancient bloomery ironmaking in
Norway’, under the chapter heading “Blooms from the Early
Iron Age” (all are from Norway):
a) Lake
Hartevatn, Bykle, county of Aust-Agder
Reference :
#00/187 - University Museum of Antiquities
now at The Hovden
Museum of Iron Production, Bykle
https://hovden.com/tellus/hovden-museum-of-iron-production/?lang=en
Date is not given
Dimensions not
given
Weight of 22.54 kg
Density of 4.6
gm/cc
Figure 5 : From Espelund, 2013, pg 47
Looking at the image presented, the top
surface of the bloom is shown, with what is most likely the
tuyere side to the bottom of the image. The outside surface
shows many irregular ‘spikes’, which certainly suggests this
bloom was not compressed by hammering beyond removal of any
clinging slag. The slight depression in the upper surface
suggests the bloom was sitting quite high in the furnace, so
that the upper part was exposed to erosion effects from the air
blast hitting it.
b)
Modum, County Buskerud
Reference :
#AKS-61 - Museum of Cultural History, University of Oslo
now in a private
collection ‘at Kjølstad’
Date is not given
Dimensions :
thickness at 12.1 – 12.4 cm, diameter at 23.1 – 23.8 cm
Weight of 17.89 kg
Density of
5.36 gm/cc
Figure 6 : From Espelund, 2013, pg 48
Again, the orientation of the image is with
top shown, tuyere likely to be to the bottom of the image. The
upper surface is flatter, so likely a better position within the
furnaces in terms of the effect of the air blast. The surface
does show some flatter areas that might be the result of initial
hammering, but still the overall shape is quite ‘lumpy’, which
suggests minimal compaction at best.
c) Hira
/ Asket
Reference : #T-21
175 – NTNU University Science Museum, Trondheim
Date is given (via
C-14) as 760 – 410 BC
Dimensions are not
given, but estimated from scale as about 21 cm wide by 24 cm
long
Weight of 17.2 kg
Density of 4.9
gm/cc
Figure 7 : From Espelund, 2013, pg 128
(described pg 48-49)
This bloom is shown from the bottom side, and
it obviously has a more bowl shaped central portion that trails
away thinner to one side. The tuyere point is likely to to right
of the image. Generally this bloom has a smoother surface, and
there are several areas that appear to show flattening (seen on
what was the bottom and to the right side)
Although three measurements is an extremely
small sample size, the average density of these artifact
blooms is 4.95 gm/cc.
METHOD
The first step was weighing each of the full
blooms or combined pieces. For masses up to 6 kg, a simple
platform digital scale was used, which provided measurements
accurate to one gram. Over this amount, blooms were placed in a
bucket and measured with a luggage type digital scale, accurate
to 10 grams. (then the weight of the bucket subtracted).
Figure 8 : Two
different scales used for bloom weight measurements.
As discussed, the simplest method for
calculating volume was used, being water displacement. Given the
wide range of physical sizes (from 1 to 15 kg), three different
containers were used, selected for closest fit to the bloom
being measured. These were filled to ‘just overflowing’ to
determine their volume capacity, so 2090 / 8520 / 12375
millilitre. The largest container, used for the largest full
blooms, was wider than high, which given the sampling method, is
likely to have resulted in the lowest accuracy (used for only
2), with those measured in the smallest (used for 17) being the
most accurate. Measurements of water volume were made using a
graduated cylinder, adding 1000 ml amounts, or fractions, added
again with bloom in place until just overflowing. These
measurements were at best + / - 5 ml of accuracy. Warm water was
used (bath temperature), both because of the low temperature of
the working space, and also to speed evaporation of remaining
moisture on bloom surfaces after immersion.
Figure 9 : Measuring volume, a bloom placed in
the mid sized container, with the graduated cylinder.
The densities were calculated, and are recorded at two decimal
places, although given the simple nature of the process used,
one place would be more reasonable.
SAMPLED BLOOMS
Figure
10 : The blooms measured in this study, including full
blooms (rear) and those that had been cut into smaller
pieces.
For this report, a total of 30 blooms were
measured, either as existing full blooms (total 13) or the
pieces composing one single, or still remaining from, an
original bloom (total 17).
Figure 11 : A 3/4 view of a full bloom, the top surface
towards the camera.
The original tuyere placement to the right. (experiment
# 9 - ‘OABA’,
May 2005)
The # 9 – May 2005 bloom provides a nice comparison to the
artifact blooms illustrated above. This bloom had been only
somewhat compacted, and had one corner (upper left in the image)
broken off for further working. The top surface shows the same
concave surface caused by air blast erosion seen in the bloom
from Lake Hartevatn (figure 5). Considered in cross section,
this bloom also has a similar shape to the one from Hira /
Asket; a central more bowl shaped core, with a thinner trailing
edge opposite the tuyere side. The surface of this bloom remains
quite irregular, with a granular texture seen in other blooms
that used the same ore type (granular hematite, a commercial
blasting grit). Although less than half the total weight of the
Hira / Asket artifact (7 kg against 17.2 kg) the actual
calculated density is slightly higher, at 5.3 gm/cc against the
reported 4.9 gm/cc.
Three samples were from experiments where it was
not possible to extract the hot bloom, so the metallic mass was
later broken free of the entire slag bowl via cold hammering.
This has resulted in a different appearance to the bloom, with a
rough ‘spikey’ surface to the top and sides, and slag containing
charcoal still attached to the bottom portions. The effect of
this on calculated density is most clearly seen on Iceland 6,
which despite one of the larger weights (at 8.8 kg) has one of
the lowest density numbers (at 4.5 gm/cc)
Figure 12 : Bottom area of a bloom hammered free from
surrounding slag bowl when cold, showing the matrix of slag
with embedded charcoal still remaining. (experiment # 60 - 'Icelandic
6', June 2015)
Almost all the blooms had been compacted to
some degree, either by hand sledge hammers (total 16), or using
the hydraulic press (total 11).
The sectioned blooms had been hot cut either
using an axe driven by sledge hammers (total 5) or via a cutting
blade on a hydraulic press (total 9). The alternative was
cutting cold, using a ‘zip’ disk on an angle grinder (total 3 –
most clearly seen in figure 3 above). Most commonly cutting
rendered full blooms into roughly 1 – 2 kg pieces and was done
for the purely functional reasons of both the on-hand equipment
sizes, and simple hand hammering ability, leading into the next
stage of the overall iron making process, rendering raw blooms
into finished working bars.
Figure 13 : Bloom sectioned using an axe driven by hand
sledge hammers. Note that one piece had been further
compacted. (experiment # 38 - ‘Icelandic
3’, Oct. 2008)
Figure 14 :
Bloom first roughly hand hammered, then sectioned using the
hydraulic press, with two pieces (bottom) further compacted
via the press. (experiment # 88 - ‘Icelandic
P3-A’, June 2021)
The DATA
Two blooms have been removed from the final
averages, reducing the data set to 28 samples. An earlier error
in labelling had resulted in two different objects marked ‘Oct.
2016’. Both appear as complete blooms, (a combined total of 6
kg) but more detailed notes describing that smelt indicate a
much larger bloom mass (total at 8.8 kg), that photographs
clearly show as almost completely sectioned into two haves. The
calculated density for sample marked Oct. 2016 A (a low
value at 4.3 gm/cc) both falls well short of the overall range,
and most significantly is quite different from that marked Oct.
2016 B (a high value at 7.1 gm/cc). This is certainly
unlikely if these were half portions of the same bloom.
The 15.9 kg bloom created from experiment #
87 (65 for 65) has been removed from the calculation of
average bloom weight (only). This is because of the large total
amount of ore used was over double the typical, at 65 kg (over a
wide mixture of ore types). (19) It is included in the other
averages however.
The full chart of weight and volume to
density, with data on ore, air and bloom type is available as Appendix One. The data for
individual smelt / blooms is seen arranged in order of
increasing density, with Oct. 2016 A, Oct. 2016 B (red) and 65
for 65 (blue) separated. The three artifact blooms are indicted
(green) Those values considered estimates shown in italics. The
blooms illustrated here indicated (tan).
Preliminary results : Bloom Average
Density of 5.98 gm/cc (28 samples) against an average
weight of 4.6 kg and average volume of 850 cc. Over this sample
set, the average ore to bloom yield is 26%.
Looking at Plotted Data
In the following discussion, the scatter
plot diagrams were prepared by Neil Peterson
from the larger data set.
Chart A : Blooms by Mass and Density
There is a clear relationship shown between
decreasing bloom weight to increasing bloom density. As
suggested in the earlier practical discussion, this would be
expected as an effect of hammer compression, where the force
applied remains relatively constant (sledge hammer blows) but
the resistance to compaction will decrease as blooms get
smaller. An unexpected observation in the charted data is what
appears to be three groupings (illustrated by coloured ovals).
Chart B : Compaction Effects
The effect of the amount of compression is
also seen when the after extraction treatment of individual
blooms is charted against density. There were only two blooms in
the sample set which did not experience any consolation process
(both broken free of encased slag after cold) and both of these
are found on the extreme lower end of density numbers. Both
those blooms worked with hand sledge hammers (total 14), and
those worked with both hand hammers plus the use of the
hydraulic press (total 10), show considerable range in density
numbers. Those subjected to the second compression effect of the
press (even if at lower heat ranges) show a clear drift to the
higher calculated densities. This is pretty much the pattern
that would be expected.
In an attempt to further understand the
variation in densities, the mass against density data was
plotted against a number of other elements considered possible
influencers.
Chart C : Ore Iron Content
It is known that iron content of the ore will
directly impact on the overall production of blooms, but in this
series, only ore of suitable qualities had been used. Very
loosely, there were two main groupings of ores used for the
measured blooms. The most frequent ore used (after Spring 2008)
had been several slightly different mixtures of the team’s red
iron oxide (Fe2O3) ‘bog ore analog’, with iron concentrations
averaging 52 % (ranging from 51 to 54 % over 14 samples). There
is a second grouping of ores of various types, all of which are
recorded at 65 % iron content (6 samples). One outlier used
granular hematite at 68 % (Fe3O4), with a number of samples not
having recorded iron content.
From this chart, it would appear that there
is a very slight indication that the ores with the higher iron
content had in fact resulted in blooms in the lower density side
of the range. This is unexpected, enough so that other factors
are suspected as the cause. Typically the smelts using the
higher iron content ores were also those using larger ore
quantities, which in turn created the larger individual blooms,
so those least to experience additional compaction through
hammering. This might also suggest the largest blooms in this
report are most similar to the even larger artifact samples.
Chart D : Effect of Air Volumes
It has been mentioned how Sauder &
Williams had demonstrated that higher air volumes, even with all
other factors remaining constant, will greatly increase not only
furnace yields, but also the density of blooms created. Their
‘ideal’ had been given as 1.2 to 1.5 litres each minute per
square cm of cross sectional area at tuyere level
(L/min/cm2).(Sauder & Williams 2002) The influence of
meeting and working with the pair, starting in Fall of 2002, is
clearly seen in the use of high volume air in almost all of this
team’s experimental work.
When the surveyed bloom densities are charted
against the rough average air volumes used to create those
blooms, this effect is the most clearly seen of any of the
potential effecting elements. Those smelts with air volumes
below 1.2 L/min/cm2 are grouped towards the lower densities,
those in the range of 1.2 to 1.4 L/min/cm2 show grouped to the
mid range, and those with air above 1.4 L/min/cm2 tend to the
higher densities.
Chart E : Experience
The blooms measured ranged in creation date
from March 2005 (experiment # 8) to October 2021 (experiment #
90). A general assumption was, that over time, the working team
would gain experience, so that blooms should increase in
‘quality’. As already detailed, employing similar furnaces, ores
and air amounts, the two aspects that might be expected to
improve would be overall yields and effective densities. Looking
at the plotted densities against creation dates, there is a bit
of a weight of the earliest smelts to the low end and the later
efforts to the higher end. The spread within each of the 5 year
groupings still remains quite wide however. This spreading
effect may have as much to do with the nature of the individual
and series investigations progressing into more and more
specialized furnace designs as time progressed.
OVERALL CONCLUSIONS
The density of solid wrought iron bar is
given as 7.75 gm/cc (20)
Obviously this is a fully compacted
state, so depending on what losses could be expected rendering
blooms into bars needs to be reflected in any comparison.
The sample size of artifact blooms with
reported density is extremely small (Although it should be noted
that a number of museums were contacted with a request for
measurements from their collections, no further information
proved available.) At least superficially, the artifact blooms
reported here show a range in density of 4.6 to 5.36 gm/cc, an
average of 4.95 g/cc. The blooms measured in this report range
from 4.45 gm/cc to 7.28 gm/cc, an average of 5.98 gm/cc (over 28
samples).
Comparing total mass to calculated density, it is clear that the
largest blooms measured are to the lower density values. In this
it might be most realistic to compare the artifact samples to
the 7 blooms ranging from 6.97 to 9.14 kg, although
bearing in mind that the artifacts are all double these weights.
This group ranges in density from 4.41 to 5.52 gm/cc, an
average of 4.94 gm/cc, basically identical to the artifact
samples.
Looking at the various data plots, two elements show clear
influence on bloom density :
The
first is the compaction process upon extraction; basically the
more effective this was, the more internal voids could be
compressed and contained slag expelled. There is a slight
difference seen between those blooms just hand hammer worked
at welding temperature, and those that that were then
further subjected to a secondary compression at an orange heat
via the hydraulic press. As the methods and equipment used is
relativity consistent, so will be the amount of raw impact
force applied. Any working blacksmith would tell you that
impact effect decreases as raw mass increases. So it comes as
no surprise that smaller blooms would show more significant
compaction effects, thus higher ‘finished’ densities, even
after a single working heat cycle.
It had already
been demonstrated, and certainly re-enforced by the
experiments over the last 20 years by this team, that
increased air volumes produced not only higher overall yields
(so bloom weights) but also an increase in density. This
effect is also seen when density is charted against air
volumes used. The average (over 16 data points) is 1.37
L/min/cm2 (an average total of 755 L/min inside furnaces
averaging 27 internal diameter). There is a major
consideration outstanding over how closely air production from
modern, high volume electric blowers matches to air produced
by various historic human powered bellows systems. Work on
this aspect continues, specifically focused on possible Viking
Age prototype bellows. (21)
Taken all together, the information in this
report hopefully should serve as a rebuttal to a disparaging
statement made at the 2008 'Iron in Thy' (Denmark) symposium :
'Modern experimenters are unable to produce iron blooms
of similar quality to those made by the ancient iron
masters'
Images :
The three images from ‘The evidence and the secrets of
ancient bloomery ironmaking in Norway’ are by Arne
Espelund, and have been scanned directly from a print copy
of his book (thus the lower quality) These used without
permission.
The charts used were prepared by Neil Peterson.
Unless specifically credited, other images by Darrell Markewitz
Notes & Citations
1) Full documentation of individual experiments found at : Experimental
Iron Smelting :
2) An illustration of this method, first demonstrated to me by
Micheal Nissen, can be found in the report on Icelandic
3 - Work Dynamic Test, October 2008 :
3) Markewitz, D., 2012 : “If
you don’t get any iron ...” - Towards an Effective Method
for Small Iron Smelting Furnaces. EXARC Journal,
Issue 2012-1
4) Description of ‘split blooms’ can be found in Pliener, R.,
2000, ‘Iron in Archaeology - the European Bloomery Smelters’
, pgs 238 – 243
(now available as a downloadable
PDF)
5) The reference time frame was chosen to fall between use of
‘Roman’ large sized (passive air draw / slag pit) and Medieval
water powered equipments (huge bellows and mechanical trip
hammers). Using a furnace similar to the ones detailed here,
working in March 2008 Lee Sauder and Michael McCarthy
were able to create a massive
80 kg bloom by adding to the top of the same mass over a
total of four individual smelts.
6) Sauder, L., & Williams, S., 2002, A Practical
Treatise on the Smelting and Smithing of Bloomery Iron,
Historical Metallurgy 36 (2), (available
as pdf)
7) Markewitz, D., 2022, Wind & Weathering : air delivery
and long term erosion - Part
2 : Wind,
8) In fact, there are no known artifact bellows even as
blacksmithing equipment from the period. (Pliener, R., 2006,
‘Iron in Archaeology – Early European Blacksmiths’, pg
131) Even as historic illustrations, there are is very little
direct evidence – and none for actual iron smelting operations.
9) Rehder, J.E., 2000, ‘The Mastery and Uses of Fire in
Antiquity’.
10) See the discussion of the use of a Norse style bellows and
the imact on bloom formation in Markewitz, D., 2014, ‘An
Iron Smelt in Vinland : Converting Archaeological Evidence
into Practical Method’ in"Can These Bones Come to
Life?", Cramer (editor) 2014.
(an expanded version is available
as a PDF)
11) Experimental partner Neil Peterson has been slowly
increasing his skill and knowledge of working with iron blooms.
Neil has been coming up and undertaking afternoon workshop
sessions were he has been taking bloom pieces in the 500 - 800
gm range and compacting these down into finished working bars.
It should be noted that this still is different than sledge
hammer work - ‘striking’ is it's own separate skill set (and one
that I also have rarely done!) On rare occasions various working
blacksmiths have joined in and contributed their skills during
initial compaction.
12) This figure of ‘8 kg ore to establish effective bloom
creation’ is considered quite important. Far too many
archaeologist experimenters undertake smelts using even smaller
amounts, then centre their evaluations on the waste slag
created, not on the production of a viable mass of iron.
13) “It must be borne in mind that before the iron in any bloom
could be transformed into usable artifacts, losses were
unavoidable in course of reheating and forging, reducing the
amount of metal so some 40 – 80 % of the original weight “
(Pleiner, 2000, pg 245)
Peter Crew, one of the first researchers to undertake repeated
and extensive experimental smelts, had initially reported bloom
to bar losses in the range of 50%. Crew, P. & Salter, C.,
1991, ‘Comparative Data from Iron Smelting and Smithing
Experiments’, in Material Archaeology XXVI
(available
as a PDF)
The work here at Wareham has so far concentrated on smaller
pieces of these blooms, typically 500 – 1000 gms, from a very
wide distribution of starting ore types, using the smelting
methods described here. In the hands of a skilled blacksmith (40
years experience), the average returns have been ranged from 60
to 80% return of bloom into working bars. It needs to be noted
that this work is being undertaken using a coal forge, and with
use of an air hammer in the later stages. Also that effectively
forging blooms requires its own set of skills. (Tests are still
ongoing against a potential future report)
14) This distortion in perception is especially seen in the
recent interest in the North American blacksmithing community,
were the initial exploration of creation and use of bloomery
iron became dominated by blade makers. The question of
‘How can I make ore into iron?’ very quickly became ‘How can I
make metal with these specific alloy characteristics to use for
knives’.
15) The best example here would again be Pleiner, 2000. Although
dozens of blooms are reported by weight and diameter, and many
illustrated via scaled drawings, there are no densities listed.
16) Pleiner gives this number as known from Europe :
“To date
(2000), more that 500 blooms or their separated parts, coming
from 90 archaeological sites have been identified.” (Pleiner,
2000, pg 243).
Given that this
reference spans from 8th century BC (‘Late Bronze Age’) to the
14th century (Medieval), this is still not a large number of
objects.
17) David suggested the ‘AccuPyc II’
as one such available system. (At a purchase price of about
$18,000 CDN!)
18) The effective start of this technology, the CAT scan,
dates to the early 1970’s, and even as large hospital use
equipment, did not become more wide spread before the early
1980’s. Archaeologist were quick to see the huge value in
scanning certain materials, especially mummified remains.
Laser scanners did not become wide spread in engineering /
industrial application until into the early 1990’s, (partially
because of computing limitations). Those were large
view ‘field’ units (now commonly used for survey work at
archaeological sites)
(Trying to determine when small scale / desk top type units for
object scanning were first commercially produced proved
difficult. Units of suitable size are now easily available, and
computers powerful enough to run the data also typical. Current
price range appears to be roughly $1000 CDN)
19) ‘65
for 65’ was a mounted as a special celebration to mark my
65th birthday. Individual ore types were added roughly in the
order in which these had been employed over the previous 20
years of experimental iron smelting, the majority in 6.5 kg
total amounts. The total ore amount of 65 kg was 30 % larger
than the next largest smelt, and over double that typically
used. The bloom created, at 15.9 kg, is 40% larger than the next
largest measured here (experiment # 52 - ‘Celtic’,
August 2012, at 9.1 kg).
20) https://www.engineeringtoolbox.com/metal-alloys-densities-d_50.html
21) There are two different lines of investigation implied :
Since
artifact blooms are clearly large, does this indicate a
different overall smelting sequence was followed historically?
Or
that there were (unknown) bellows equipments used that
actually produced higher air volumes?
This compounded by a
possible difference between the ‘pulsing’ air delivery from
certain bellows designs, opposed to the constant blast from
electric blowers. The most recent experimental test was
experiment # 90 - ‘Wind
& Weathering', October 2021
Unless otherwise indicated :
All text and photographs © Darrell Markewitz,
the Wareham Forge.