A separate short photo essay on
the build.
The smelt itself would use the proven red iron oxide based
analog developed by
DARC.
(for
details)
A quantity of oak charcoal remained on hand, which had been
previously broken for size. This had been stored out of doors
since last fall however, and so was expected to have absorbed
considerable moisture. Past weights of the standard bucket used
for measuring charges was typically 1.8 kg, when this fuel was
measured at this experiment, the weight was found to be 2.0 kg
per bucket. Although this does represent a considerable moisture
content, the furnace stack height was expected to drive off any
water contained with waste heat at the top. A new source for
charcoal had recently been found, this material was freshly
made, primarily from ash, so was both bone dry and a lighter
density, at 1.72 kg per bucket. The expectation that any
contained moisture would not seriously impact the individual
burn rates was born out in so much as there was not any real
effect of shifting charcoal type about half way through the main
ore addition sequence.
Considering Air :
The expectation was that the combination of lower air volume and
the pulsing delivery would extend the individual charge burn
rates, certainly the situation seen with past smelts using the
human powered smelting bellows. For this reason, the pre-heat
phase was started earlier than normal (8 AM) and ran slightly
faster than normal.
The ideal would have been to provide for measurements of
delivered air volume over short interval times for as much of
the experiment as possible. Currently there are three different
meters available, but each of these has problems with accuracy.
Most notable being that the measuring element of the (expensive)
Omega HHF1000 was not producing readings. With no dependable
instrumentation on hand, it was decided not to include any at
all.
Complete air supply system : blower /
gate / sliding plate / view port / tuyere
Considerable discussion was ongoing about how much air was
actually being delivered into the furnace. The readings from
smelt 90 had indicated an average of 520 LpM was being
delivered. Normally the air from the electric blower is
controlled via a movable plate on the output side, which had
been very roughly marked with lines at 100 LpM intervals. These
increments were considered an estimate, and at best most
valuable as a direct comparison from one smelt to another (we
set at 800 last time, set again at 800 this time). During smelt
90, the more accurate Omega HHF 1000 unit had shown that any of
the individual line / values were in fact only 84% of the true
delivered volume.
Knowing at least the form of this, even if lacking the exact
detail of changing volume over time, it was decided to increase
the flow at the blower outlet with the expectation that the
actual delivery to the furnace would be a lower amount through
the sliding plate mechanism. Initially (working without
consultation) the output was set at 600 LpM at the initial wood
pre-heat and first charcoal additions. In retrospect, this would
have been really only 500 LpM,
less what additional
effect the sliding plate created. (It is worth remembering that
the 'ideal' high production volume for a 25 cm ID furnace would
be 580 - 880 LpM.) (for
details)
In discussion, it was decided to apply a variable of 70% against
the reduction impact of the sliding plate, so air was increased
to 800 LpM with the expectation this would result of a delivery
of 560 LpM to the furnace. Once again, applying the calculation
of blast gate inaccuracy, this potentially would mean a flow
closer to 470 LpM delivered.
Later in the smelting sequence, against the extremely long
charge times / burn rates, air at the blower would be increased
to 900 LpM at the blower, potentially 530 at the furnace. This
change was made at 5 hours into the overall burn, with 5 kg of
the total 17.5 kg of ore added.
the Smelt :
Team:
Darrell Markewitz - smelt master
Neil Peterson - lead hand
Kiernan Rodgers - charcoal / ore additions
Richard Schwitzer - striker
Sarah Scroggie - additional photographs
Pre-heat time : 2 hours
Total smelt time : 10:37 (plus extraction)
Ore addition time : 402 minutes (6:42)
Charcoal burn rate :12.1 min/kg (during ore)
Ore addition rate : 23 min/kg
The
established method of
adding a quantity of iron rich tap slag as starting charges, 1
kg amounts against charcoal bucket was used to a total of 2.8
kg. By the time it was estimated the first two additions (1.8
kg) had settled to tuyere level, it was obvious that the slag
bowl was forming both too high and too close to the tuyere. It
was observed that there was considerable venting of air from the
sliding plate due to the required loose fit to the mechanism.
The concern was that this was resulting in a loss of applied
pressure to the input air - which in turn was not correctly
forcing air into the body of the furnace. This problem was
considered less likely with an actual bellows system used, as
workers could have been instructed to simply apply more pressure
on the down stroke to compensate.
Field drawing - observed position of the slag bowl, early
in the smelt
Several attempts were made to reduce liquid slag level
(observable down the tuyere) by probing down with a steel rod
and punching a hole through the developing slag bowl. At four
hours into the smelt, with both tap slag and 3 kg of ore into
the furnace, it was decided to pull open the arch bricks and
attempt to lower the bowl. The charcoal fines base was scooped
to expose the slag bowl, which was seen to have formed fully
only over the front half of the furnace. First the bowl was
punctured from the bottom, in an effort to drain excess (??)
slag to below the bowl bottom with the hope this would allow the
bowl to sag into the open base. This did not prove entirely
successful, so in a more aggressive intervention, a heavy bar
was used to punch down from the top of the furnace to push the
entire bowl downwards. This, combined with the increase in air
volume mentioned above, did allow the smelt to proceed without
further problems with serious air blockage.
Overall, the individual burn rates were excessively long, the
average time per standard bucket (roughly 2 kg) at over 30
minutes, in the range of three times the time considered normal
for a high volume via electric blower smelt. Because of these
long times, the charcoal was probed several times, on each
occasion resulting is a significant settling. It appeared that
there was a hollow area developing just beyond and above the
tuyere, again not normally the case.
Ore additions were increased as was the usual method, first 1 kg
/ 1.5 kg / 2 kg with a last at 3 kg per charcoal measure.
Because the entire smelt effort had already been in progress
some 12 hours, it was decided to start the burn down 17.5 kg
total ore. As the furnace burned down, it became obvious that
the air had not penetrated fully across the internal volume, at
least at the lower (tuyere level) part of the furnace.
Ignition in the interior, tuyere to the
left
There was some difficulty on extraction. Although an attempt was
made to 'thump' the bloom loose in place within the slag bowl,
both the bloom and slag bowl proved very difficult to break
loose of the furnace. In the end, this combination with poor
build technique resulted in the furnace breaking apart into the
individual 'brick' additions.
Remains after extraction
image by S. Scroggie
On extraction, it appeared almost as if there were two separate
slag bowls. The initial mass, which had been pushed early in the
process, had stayed attached to the tuyere side, with a second,
more conventionally shaped mass above it. Part of the difficulty
in extraction was that the bloom itself was not freed from the
slag, so the entire interior was pulled clear as one block. This
double lobed shape can be seen if you look clearly at the final
stages of this
video of the
extraction (
video by S. Scroggie). As the cleaning
and compaction hammering was undertaken, this large block would
break off entirely and later was found to contain no appreciable
iron. The upper slag mass would however contain a reasonable, if
fragmented in texture, 3 kg iron bloom.
Total Charcoal : 48 kg
Total Ore : 17.5 (analog at 10% moisture)
Bloom : 3 kg
Yield : 17 %
Condition : fragmented
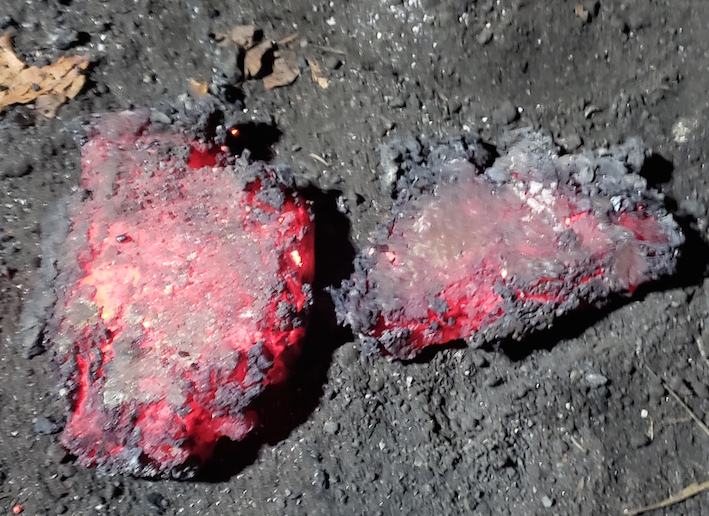
|
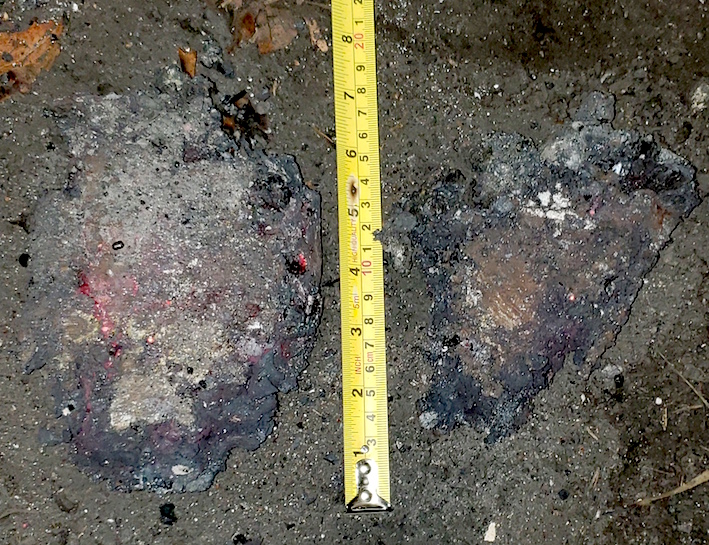
|
Bloom flattened / hot
image by N. Peterson
|
Bloom against scale
image by N. Peterson
|
Discussion :
The chart bellow compares the results here with previous uses of
the on hand smelting sized twin bellows. All these tests use the
DD1 bog ore analog and similar size and layout of the furnace.
SMELT
|
AIR DELIVERY
|
BURN RATE |
ORE
|
YIELD
|
#42 - Vinland 3
|
norse
smelting bellows
|
6.3 min/kg
|
18
|
16 %
|
#44 - Vinland 5
|
norse
smelting bellows
|
8.8 min/kg
|
20
|
14 %
|
#63 - SCA 50
|
multiple norse
blacksmith bellows
|
17.6 min/kg
|
22
|
25 %
|
#73 - SCA FOOL
|
norse
smelting bellows
|
12.5 min/kg
|
30
|
18 %
|
#74 - Iron at
Vinland
|
norse
smelting bellows
|
11 min/kg
|
28
|
20 %
|
#90 - Wind
&
Weathering
|
electric reduced
volume
|
7.4 min/kg
|
32
|
31 %
|
#91 - LAM,
Lower & Longer
|
(limited sliding gate)
electric reduced volume
|
12 min/kg |
25
|
28 %
|
#92 - Lower
&
Longer 2
|
electric reduced volume
|
18.1 min/kg
|
22
|
20 %
|
#94 - Pulsing Air |
sliding gate / electric
reduced volume |
12.1/kg |
17.5 |
17 % |
Comparison : norse smelting bellows to reduced
volume
/ electric blower
Ore amounts shown, as larger amounts typically produce
higher yields.
It is important to note that previous attempts to directly
measure air volumes into smelting furnaces have suffered from
the nature of the instruments available for this purpose, the
results often inconsistent and conflicting.
Measurements taken using a smaller blacksmithing scale version
of the Norse twin bellows by Peterson showed that air output via
this type of unit delivered a distinctive double peak variation
in flow over time. (Peterson, 2021). This may be due to
construction differences between the two sides, or possibly the
differences between right and left hand strength.
Showing the theoretical delivery air
volume from a Norse Blacksmithing bellows.
Output measured by lifting a weighted float.
Interval determined from video recording.
(Altered to match curves to time)
The following is based on part of an extended discussion on
Facebook
Iron
Smelters of the World, sparked by comments from
fellow researchers
Rom Bohr / (and old friends)
Lee Sauder /
Jens
Jørgen Olesen.
Evidence from Viking Age for bellows is a problem. Only two
existing illustrations, both related to blacksmithing, and no
artifacts. There is no physical evidence from iron smelting
sites for bellows construction.
Past
work has included a total of 16 smelts using three
different sizes of the Norse style, two bags set side by side
joined by Y tube. The burn rate observed (4 uses with good
records) runs an average of 9.6 minutes per kg.
In the output over time graph by Neil Peterson (above), the air
never goes to zero and there is a distinctive double hump to the
volume curve. It is understood that the specific plate shape
used here does
not correctly mimic the air volume cycle
from the bellows. We understood that it should be possible to
change the hole shape to better simulate air over time, but
since we had instrument failure, the test described here was
understood to be at best 'proof of concept'.
Why are we using this size bellows unit? The
first smelting bellows
build was producing in the range of 700 LpM, but that proved too
massive to realistically operate (I accept that build quality a
factor). So the human dynamic determined the size of the unit on
which this discussion is based. I accept the critique of
potentially poor construction.
Potentially the twin bags could be linked to long overhead
shafts (as
Jens Olesen does,
although he works a single chamber unit), rather than handles
set directly on the top plates as the historic illustrations
show (I take the critique that there is no proof that the long
handle was not done, although there might be a question about
the required framing.)
Ore used here was the same analog (Fe2O3 @52% Fe) and similar
amounts @ 25 kg. We have no access to natural bog or other ores
in Central Ontario. A realistic critique is that our ore may be
the cause of low yield (average 17% over same 4 smelts). It is
important to remember however, that using that same analog, in
basically similar furnaces, but pushing 800 - 900 LpM via
electric blower = shorter burn times, the result is consistently
higher yields and denser quality blooms (most like the known
artifact samples).
However, to paraphrase Lee Sauder ‘
If you don’t get iron like
theirs, you can not be doing what they did.’
It is worth thanking Rom, Jens and Lee (especially Lee) who
had through their questions and comments, certainly helped me
clarify my thinking around all this.
Conclusions :
1) Sliding Gate
- The mechanism of the sliding gate proved both effective and
durable.
- There were observed short periods, lasting about 15 seconds,
when the rotation rate dropped slightly. It is unknown if this
was due to stress on the motor, or the very real possibly of
variation in line current in the rural electrical system.
- There was considerable loss of delivered air pressure,
primarily due to leakage at the moving plate. No way to correct
for this was suggested, and this equipment does not well
replicate the ability to modify pressure possible in a human
powered system.
2) Reduced Air Volume / Pressure
- As with other times low air
volumes were used, either
with use of the Norse twin chamber smelting bellows or mimicked
by reduced output of the electric blower, both bloom yield and
quality was impacted. It was generally felt that despite the
very long time involved, increasing the ore amount would
directly improve both aspects.
- Delivered air
pressure into the furnace was considered
to be a significant problem however. It was clear that the air
input to heat zone system was not projected fully into the
furnace as would be ideal.
- Due to the combined effects of reduced volume and pressure, it
was felt that more frequent probing with a metal rod to settle
the burning charcoal might have improved the overall smelting
sequence.
3) Bloom Quality
- It has been effectively demonstrated that higher ore addition
smelts generally result in denser blooms. This is considered
quite important, as the end product of any smelt is not the
bloom itself, but that mass compacted into a solid working bar.
Past experience with bloom to bar has shown the fragmented and
crumbly texture of the bloom produced here would certainly be
difficult to compact to a solid bar, and would be expected to
suffer serious losses in overall finished weight.
Future Experiments? :
a) Attempt to use a higher iron content ore.
- I still have a small quantity (two 20 kg smelts?) of granular
hematite. This material is 68 % available Fe
- I have on hand one bag of black iron oxide (Fe3O4). This
material mixed as analog would be about 61 % available Fe. More
can be purchased from Pottery Supply (currently $ 62 /22 kg)
b) Build a new smelting bellows unit.
This specifically to utilize the mechanical advantage of a long
pole, operated using the upper arm pulling (so possible to
significantly increase chamber loft = produced volume)
Olsen certainly uses a single bag bellows designed on this
principle with good effect. The key would be having a unit sized
to create a burn rate closer to that ‘magic’ 6 minutes per kg.
The current unit has roughly the same plate size as Olesen’s,
but the loft distance is significantly shorter.
For sake of completeness, the next step should
be repeating this experiment :
- ensuring full measurement of
actual air volumes over time
- increasing ore amount to the more usual 25+ kg
- altering method to include more frequent probing to settle
charcoal