)
was undertaken using a well practised method, with the normally
used steel can used as an internal form. As it turned out, there
was not enough raw material on hand to create as tall a furnace
as desired. For the demonstration, a ceramic kiln support tube
was used, again something used with good results in previous
work.
Because of the build process resulting in a stack height less
than what is considered effective, a field expedient fix was
applied. A discarded metal pail had it's bottom cut off, and
this was added on top of the furnace to extend the height
potentially a further 46 cm. In practice only half this distance
was used, creating the utilized stack measurement at 59 cm.
The smelt would use the proven red iron oxide based analog
developed by
. (for
The charcoal was again that made by Ontario
blacksmith Avery Goltz. Primarily from ash, this material was
found to vary considerably in weight, ranging from 1.7 to 2.1
kg for our standard bucket charcoal measure. This most likely
due to absorbed moisture after a year's outdoor storage. An
average weight of 1.9 kg / bucket was used on the
data record.
Considering Air :
Again the expectation was that the combination of lower air
volume and the pulsing delivery would extend the individual
charge burn rates, certainly the situation seen with past
smelts using the human powered smelting bellows. For this
reason, the pre-heat phase was started earlier than normal (8
AM) with the expectation of slower burn rates into a much
longer total working day.
Complete air supply system :
blower / gate / sliding plate / Y tube to bellows / air
gauge / view port / tuyere
Because of the demonstration / teaching component of this
effort, it was decided to link the smelting bellows into the
total air system. The intent was that this would be used for
short periods, mainly as an experiencial tool, with the main
air supply being via the electric blower limited by the
sliding gate. The number of individual linked elements would
result in air losses at each point. The physical layout also
placed the view port at an awkward location, making probing to
clear any tuyere blockages more difficult.
the Smelt :
Team:
Darrell Markewitz - smelt master
Rey Cogswell - lead hand / record keeping
Kiernan Rodgers - charcoal / ore additions
Autumn - charcoal / ore additions
Mark Paisley - striker
Neil Peterson - assisting
With a larger than normal team, several new to the process,
and the added complications and distractions of a public
demonstration, keeping work process consistent proved
difficult. To further complicate the smelt, the weather
contributed high, gusting winds and several periods of driving
rain. New hands keeping the data records would lead to
interpretation problems after the fact and some loss of
information.
The period from the start of adding charcoal through to
considering the furnace burn stable enough to start adding any
slag or ore charges was greatly extended. In this case
covering almost three hours. The reason for this is criptic at
the point this commentary was written ( * ). During this
period the air from the blower was blocked and a number of
individuals would employ the twin bellows. Measurements were
made via a small (and well used)
vane
styled wind speed gauge. As this gauge is not considered
very accurate at this point, the measurements (averages) are
best considered only as comparisons :
Darrell = 35 kph
Neil = 32 - 28 kph
Rey = 29 - 19 kph
? = 35 kph
?? = 28 - 21 kph
At the end of this test, the electric blower to pulsing plate
system was initally adjusted to deliver the same 35 kph
measurement.
Most significantly, there would be two major interruptions in
electrical power. The first of these occurred just after the
first additions of ore, and would last for 7 minutes. During
this gap, air was supplied by the bellows only. In the
scramble to provide labour, along with inexperienced hands,
the net result was a significant drop to furnace temperatures.
In an effort to combat this, air flow from the blower, when
that returned, was increased significantly. although
preserving the smelt as demonstration, this would negate the
intent of the experimental aspect however.
The second interruption occurred late in the smelt, and would
hasten extraction (described below)
The
established method of
adding a quantity of iron rich tap slag as starting charges, 1
kg amounts against charcoal bucket, was used at the start to a
total of 4 kg. Also as normal practice, ore charges would
increase regularly from a starting amount of 1 kg per charcoal
bucket measure to 3 kg additions.
Pre-heat time : 2 hours
Total smelt time : 12:28 (to extraction)
Ore addition time : 297 minutes (4:57)
Charcoal burn rate :12.0 min/kg (during ore)
Ore addition rate : 11.2 min/kg
As was expected, the burn times with the reduced air volumes
mimicking twin bellows delivery being much longer than that
produced via direct input from high volume electric blowers.
This clearly marks a significant difference between historic
and modern equipment for air delivery.
The failure of electric power near the end of the available
ore amount resulted in a quick decision to rush straight into
extraction. With low experienced team members unsure how to
proceed when speed was critical, confusion was the result.
Because the exact amount of charcoal required to completely
fill the furnace was not recorded, it is not clear exactly how
much ore remained in the interior stack as the furnace was
quickly emptied. Given that charge levels were at 3 kg ore per
bucket volume, this loss would have been in the range of 9 to
possibly 12 kg of the added ore, this an amount equal to
between a third to even half the total.
Between all the delays, the furnace had already cooled
significantly when a mass, basically the entire slag bowl
itself, was eventually pulled clear about 20 minutes later.
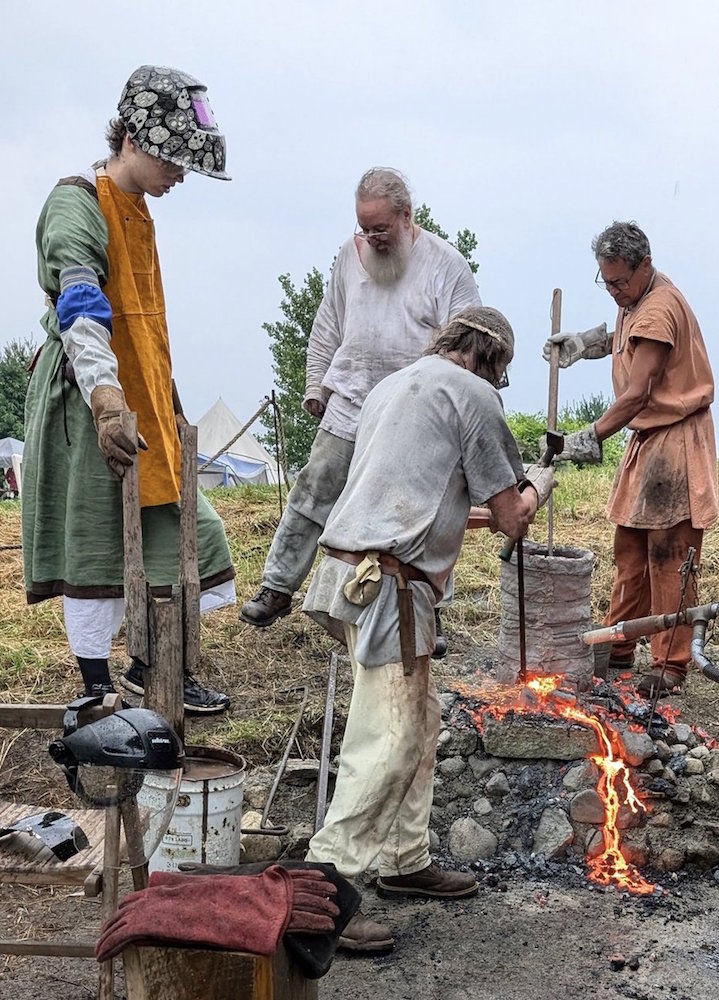
|
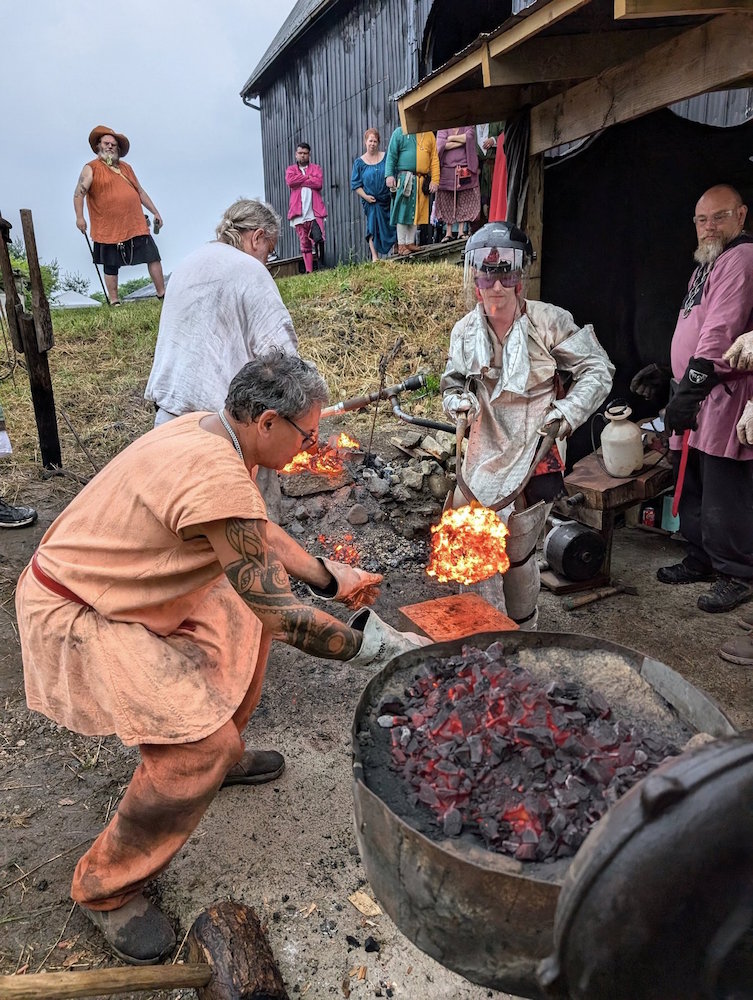
|
FAST preparation
for extraction :
Darrell (centre) breaks open the bottom arch
Mark (right) starts scooping out hot charcoal
Kiernan (left) stands by to use the Thumper
Neil (rear) gathers required extraction tools
|
Large block of slag
pulled free, with a bloom inside?
Mark (left) moving the compaction stump to
place
Rey (right) pulled and moved the mass
images by Tamara Paisley
|
Given the combination of problems with interrupted and
inconsistent air flow, significant losses due to pre-mature
extraction, it is not surprising the bloom found when all the
depicted slag was struck off was not impressive. In the rush
to move the hot bloom directly to a waiting coal forge under
Mark's hands, the normal 'after initial compaction'
measurement was not made. The best estimate was something in
the range of 2 - 2.5 kg, with the quality assessed as 'very
fragmented'. Mark's attempt to consolidate the bloom was a
huge step forward in his own blacksmithing experience. A
number of small, partially compacted pieces was the end
result.
As the losses due to the early extraction of ore never
reduced are unknown, there is no effective way to calculate
a yield. Direct ore input to bloom output would be
about 8% / more reasonable would be ore without loss in the
emptied stack, so closer to 12%.
(*) Another important failure in record keeping.
For a number of reasons, this report was written fully two
months after this event. Memory fades, so with inconsistent
written records (Willow's full name never written down as
example) and very limited photographs available,
reconstructing details becomes difficult.